- Quantity Tolerances Can Affect Your Order
Fancy 10% more or 10% less than you asked for?
It's a standard practise in the extrusion market to operate a shipping tolerance like this... But why?
The amount of billet that is selected to be pressed cannot be precisely calculated and is an educated guess. It’s based on the theoretical weight per metre of the profile, the predicted start-up waste and the size of the customers order. The result? A final quantity that could be around 10% more or less than your order size.
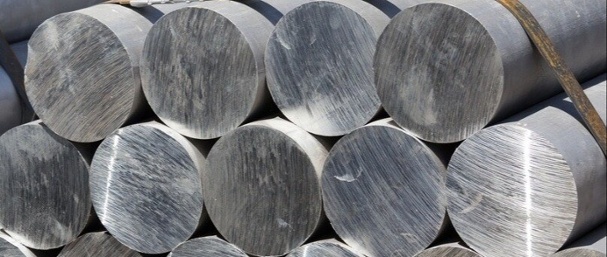
Usually any material that passes quality checks will be aged, packed and shipped. Likewise, if the order is a little short because of some scrap or poor quality pieces, the order will not be pressed again to meet the ordered amount.
This is something to keep in mind if you need a specific amount to make a kit or assembly that requires an even number of pieces. Or if it’s a one off project.
Working with an aluminium extruder who has stockholding facilities can help as they can 'call off' overrun bespoke material until the next time you need it, keeping your warehouse free of odds and ends and your cash flow free from goods you can’t use or sell.
- Die Scrapping
Most extrusion tooling has a very long life… it’s a lump of steel right? Well in theory that’s true.
But, over a longer term, unused dies need maintenance and servicing to prevent corrosion which could ultimately lead to poor surface finish and a host of other issues. Another key issue about keeping dies for a long time is the amount of space they take up.
Many extruders will scrap a die if it’s not used within a period of between 2-5 years.
Some extruders offer long-term die storage and maintenance as a service. Some have a no scrappage without notification policy. But it’s always a good idea to check the terms of your quote, especially if you know there will be a long interval between your need to use a tool.
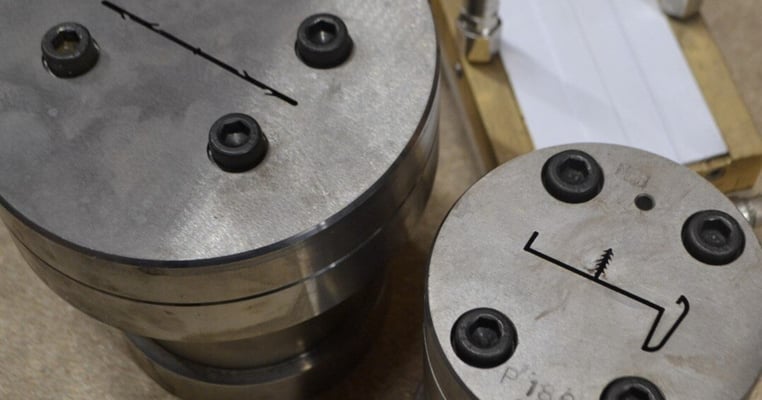
Working with an independent stockholder can give you some protection. For example, we have a stockholding facility and none of our extruders will scrap a die without notice as we have policies in place to make sure you are made aware of the costs of die storage and the risk of die scrappage upfront.
- 30-Second Sense Check
New profile projects can often benefit from a little sense check upfront, such as knowing how many metres an extrusion run will yield.
To do this, follow these basic steps:
- Work out your profile's theoretical weight per metre
- Multiply the cross-sectional area of the profile by 0.0027g/mm3 (approx. density of most extrusion grade aluminium alloys)
- For example, a 25x25x2mm angle has an area of 96mm2, so multiply by 0.0027 and 0.259 kg/m is the theoretical weight per metre
- So, if the press states a 500kg minimum order, divide 500kg by 0.259kg/m and you’ll yield 1930m of extrusion
.png?width=1800&height=700&name=Untitled%20(19).png)
Now it’s easy to work out the cross-sectional area of an angle, but what if your profile is an irregular shape? If you're working offline, try to break it into smaller shapes, work out the areas and sum them up. Most CAD packages (even the free ones), have an option to tell you the surface area of a face in a model.
But there is another way too… Simply send your sketches, drawings, CAD models, etc. to hello@bwcprofiles.co.uk and we can help you get these sorts of questions answered fast.
- Only Solids Get Pushed Through!
Did you know that aluminium is never in a liquid or molten form during the extrusion process?
The boiling point of aluminium is 660 degrees Celsius and most extrusion processes run at about 375-500 degrees Celsius. So, whilst the material is softened by the heating process it’s never a liquid and it doesn’t glow red like the hot molten metal you might be picturing running through the die.
- Check Your Tongue Ratios
When designing profiles, it's really important to avoid creating any very deep channels or recesses that have a narrow opening.
If you think about the extrusion die as the "inverse" of the profile, the area of the tool that holds the channel or recess open is called the ‘tongue’.
If this ‘tongue’ ends up very large, but is only joined to the rest of the die by a small amount of material, it becomes very fragile and under the immense pressures of the extrusion process, can break!
To explain further, check out the following image, which shows the design of a hopeful client looking for an 80x15x2 Channel.
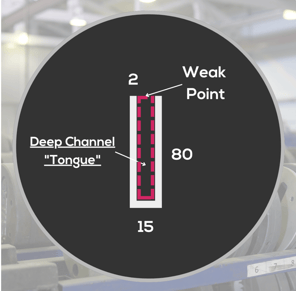
The channel depth is 78, the width is 11 so the depth is a little over 7x the width or a 7:1 tongue ratio. Without some redesign. it's not going to be possible.
A ratio of 3:1 is usually considered acceptable, 4:1-5:1 difficult, but can be done in some limited simpler scenarios by introducing large radii transitions and other techniques. Beyond 5:1 is extremely difficult and will often require a redesign or using a tear-out strip to extrude the design as a hollow.
We hope you've enjoyed our five interesting facts about extrusions! Let us know at hello@bwcprofiles.co.uk if you want anything explained in more detail or, if you have any other queries too!