ABOUT BWC PROFILES
Based in Milton Keynes, we offer a UK-wide, one-stop shop service that incorporates the design, manufacture, fabrication, finishing, stock holding, and distribution of your extruded profiles.
Our purpose-built, in-house powder coating facility with high-volume capabilities and various finishing options means we can accommodate and coat aluminium in a variety of colours and sizes... giving you that final end process to aluminium profiles.
Our In-House Powder Coating Facility
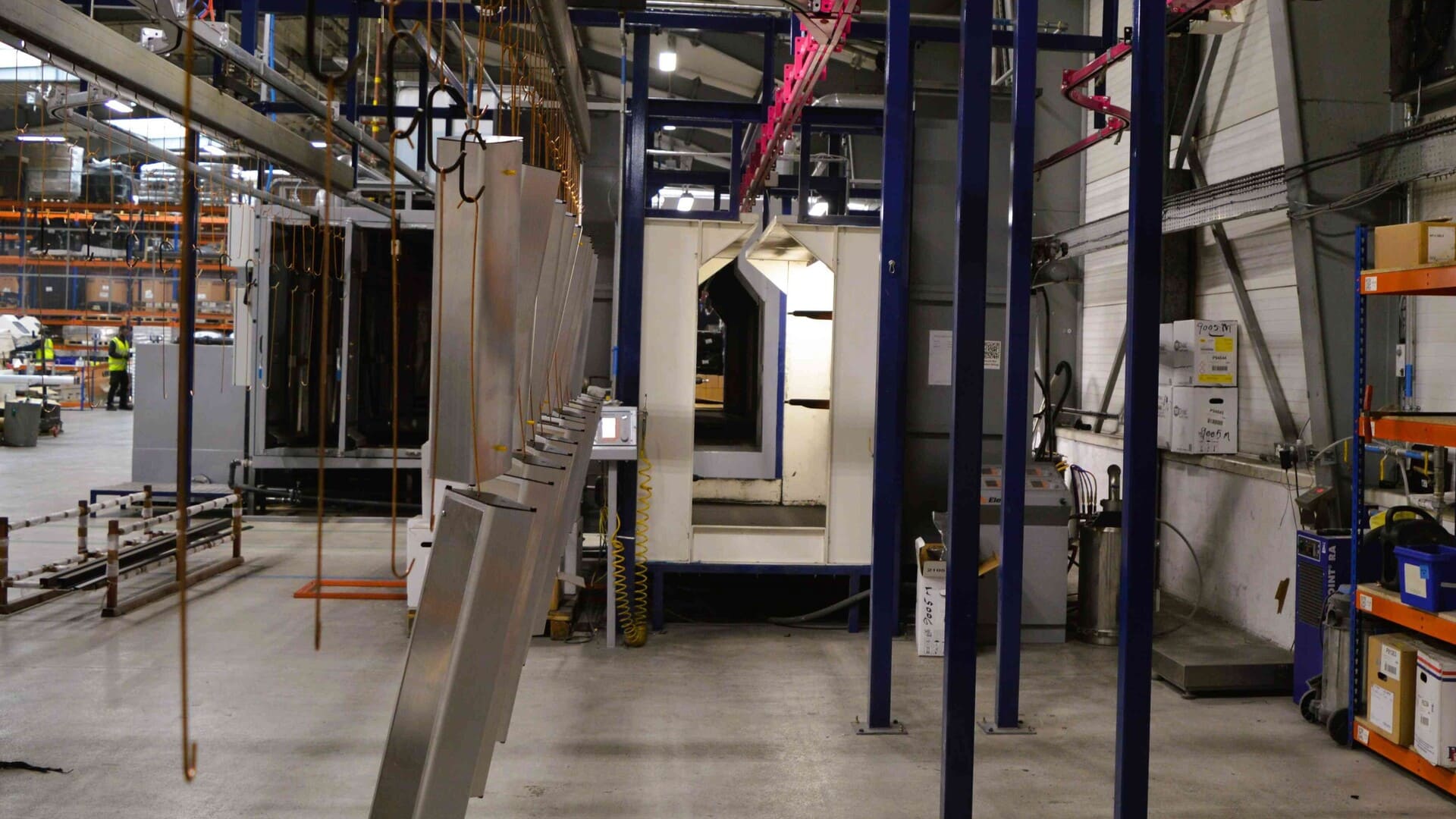
purpose built facility
Our in-house, automated, purpose-built facility, run by our dedicated team, is specifically designed to cover all your powder coating needs.
Benefits of Powder Coating
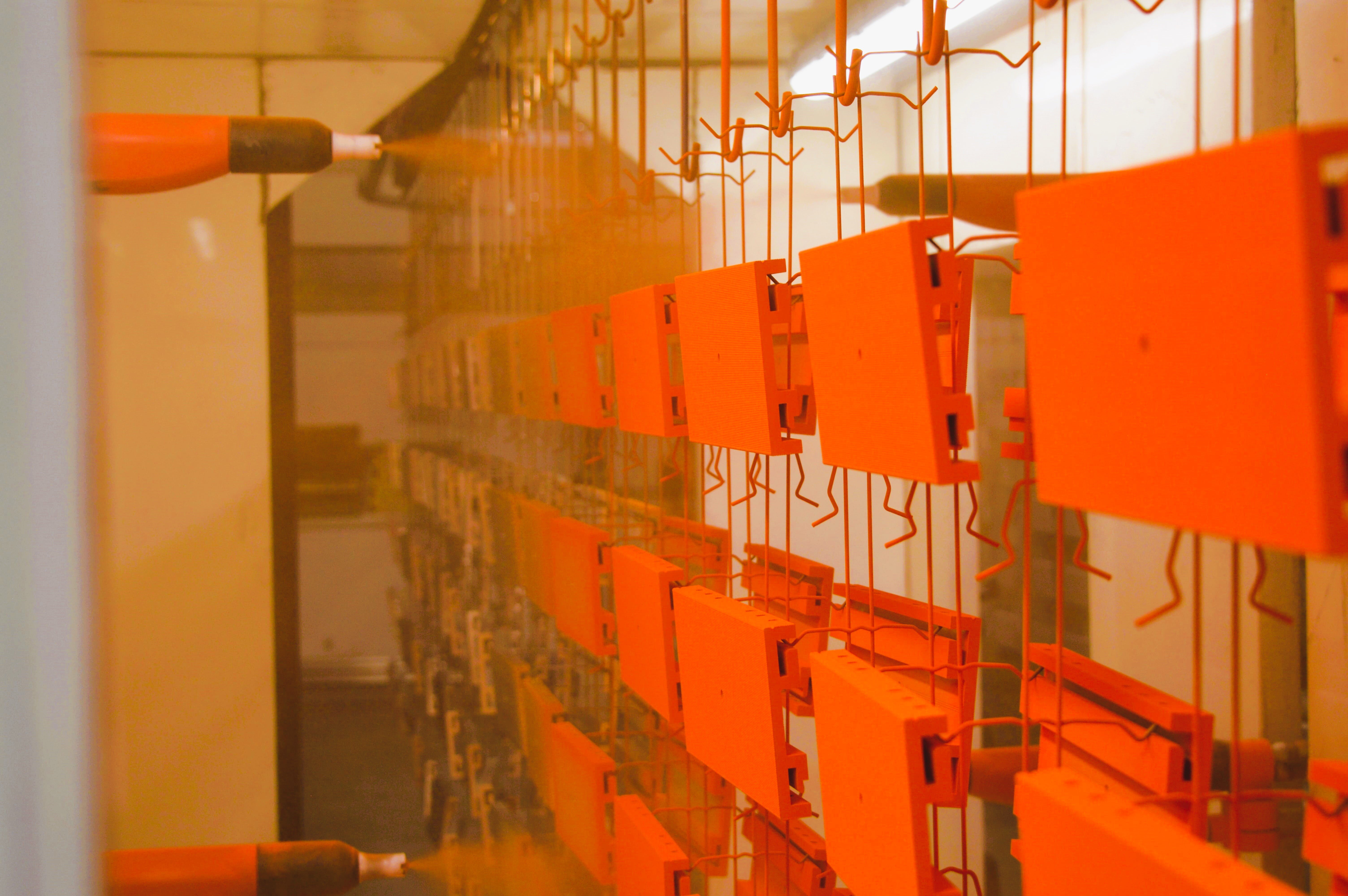
- Corrosion and UV resistant
- Easy to clean
- Electrical insulation
- Enhanced functional performance (weather-proofing)
- Solvent-free - no volatile organic compounds
- Many specific benefits to industries including automotive, agricultural, defence, commercial, marine, medical and offshore
- Seamless colour finish: gloss/texture options
- Consistency of colour between batches
- Process includes surface pre-treatment and high temperature oven curing
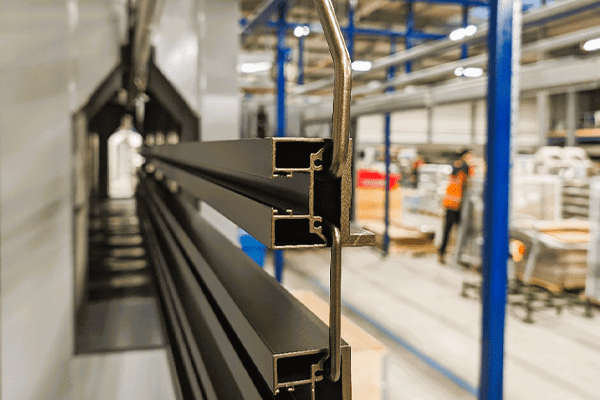
THE IDEAL FINISH
From start to finish, your aluminium profiles receive the care and attention they need with our meticulous powder coating process.
We begin with our 5-stage pre-treatment before moving to colour being applied electrostatically, then curing the newly powdered profiles under the heat of our industrial powder coating ovens (to form a hard-plastic coating) to securely packaging your goods in wrapping of your choice.
Our process is designed to ensure that your aluminium profiles get everything they need for a colour durable finish, alongside that extra layer of wear, UV protection and smooth, aesthetically pleasing colour.
THE PAINTLINE PROCESS
DEDICATED POWER COATING FACILITY
Our purpose-built, in-house powder coating facility (with an automatic conveyorized system) is designed to provide the highest quality finish to your aluminium profiles.
The powder coating process starts at our in-line treatment tunnel, which comprises of five stages of pre-treatment - critical for paint adhesion and longevity - before moving to our automatic, horizontal paint line that can accommodate aluminium profiles of 6.5M (length) x 1.3M (drop) x 0.4M (width).
We also incorporate high quality line systems and hanging applications called Hang On accessories to help maintain a consistent pattern during the paint process. This also allows for cost-effective density (without any compromise to quality) and for all kinds of shapes to be hung efficiently and profiles kept locked in place.
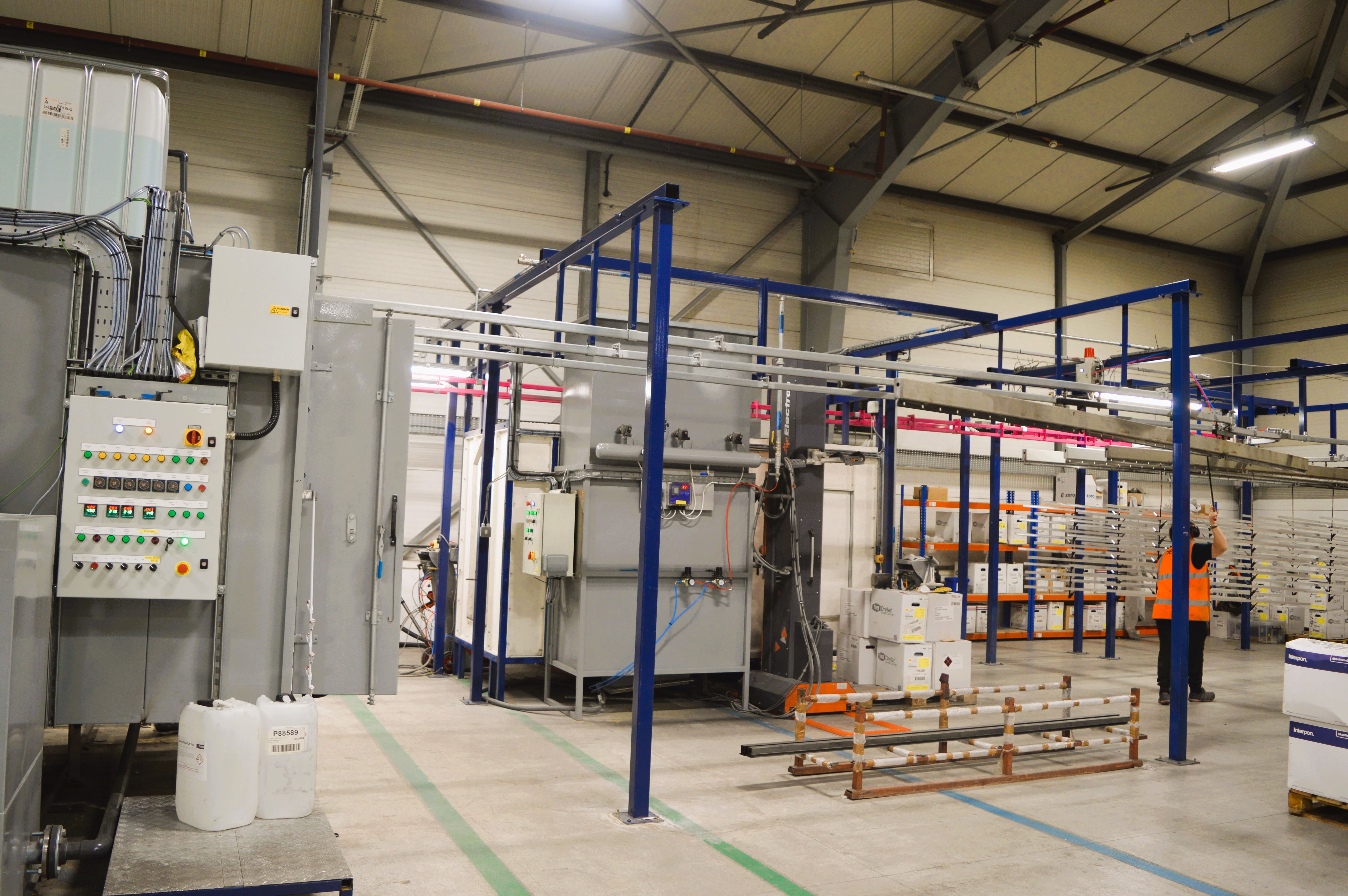
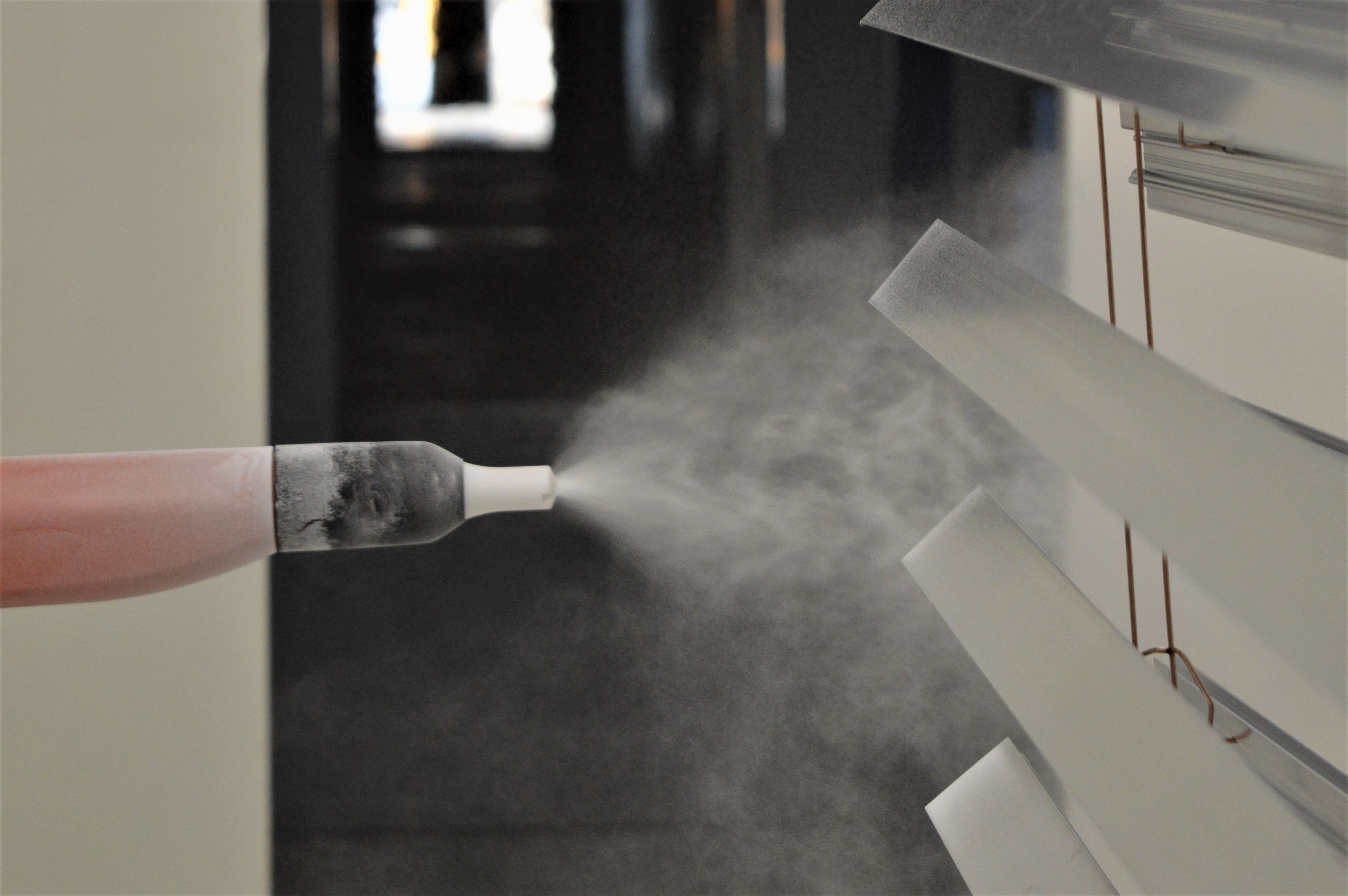
THE POWDER COATING STAGE
Powder coating comprises of finely ground resins and pigments. Available in a full range of colour options, our powder coating is automatically applied via electrostatic spray guns.
This means the spray gun applies a charge to the powder during the spray process, which ensures the powder can 'cling' to the electronically grounded (aluminium) component.
The next step is known as the 'curing process'. This is where the powder melts and chemically transforms to a continuous film by heating at high temperatures (typically between 180C and 200C). This ensures the durability and longevity of the applied powder film.
THE POWDER COATING PROCESS
Powder coating comprises of finely ground resins and pigments. Available in a full range of colour options, our powder coating is automatically applied via electrostatic spray guns.
This means the spray gun applies a charge to the powder during the spray process, which ensures the powder can 'cling' to the electronically grounded (aluminium) component.
The next step is known as the 'curing process'. This is where the powder melts and chemically transforms to a continuous film by heating at high temperatures (typically between 180C and 200C). This ensures the durability and longevity of the applied powder film.
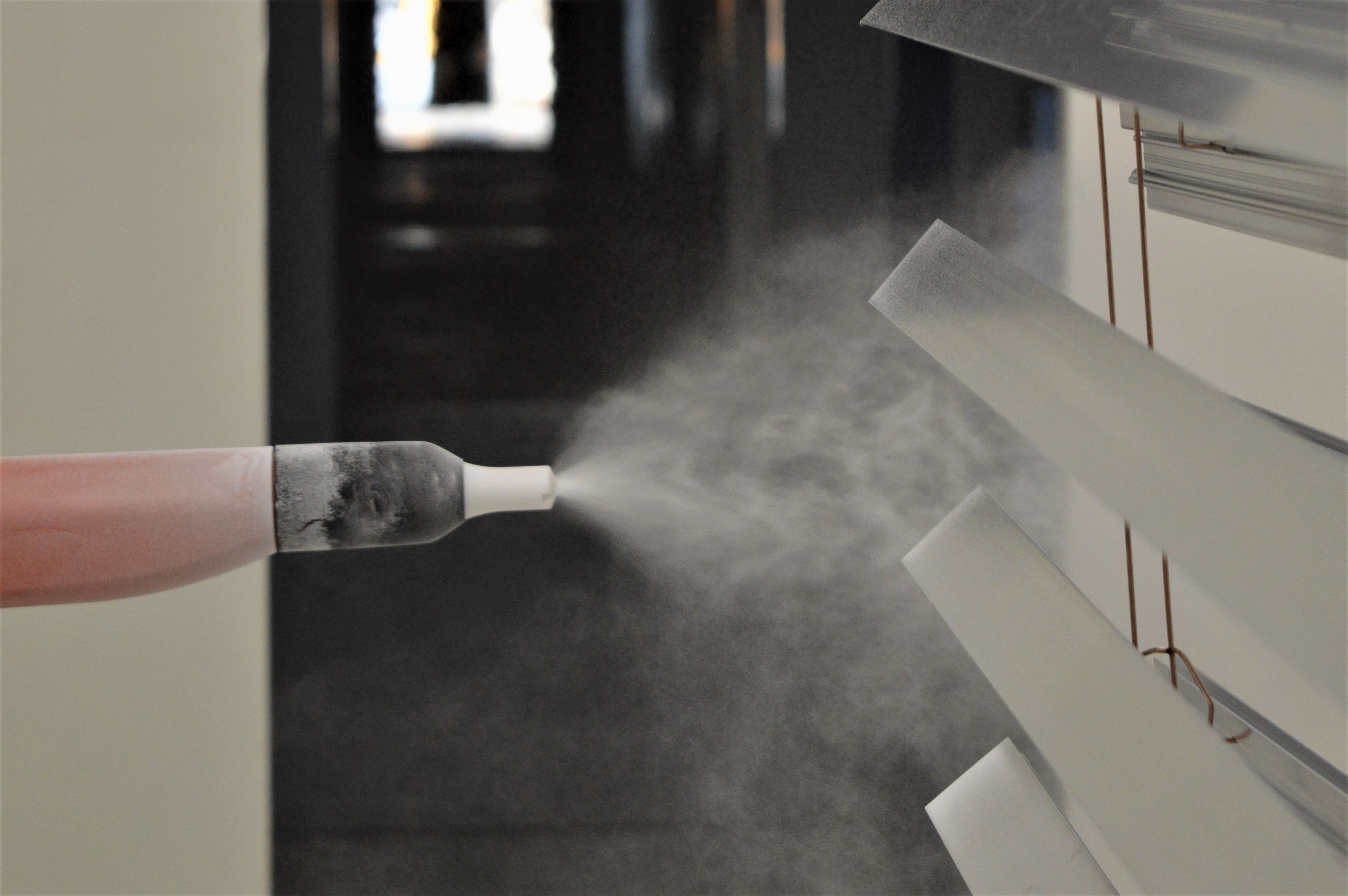
OUR PROFESSIONAL TEAM
Our close-knit team of powder coaters have years of experience in the field and they pride themselves on providing a first-class, professional service.
The personal, hands-on approach of our team makes a real difference to your powder coating order, and because our service is bespoke, we are able to inspect profiles after pre-treatment and before and during the painting process, alongside additional services such as masking or threading (ideal for customers in lighting or electrical who need critical areas free from paint) and hand-spraying profiles.
To ensure we provide the desired finish and high quality control, our team implements end of line testing and inspection by applying a Micron thickness gauge, gloss metre and cross hatch, scratch testing. All finished profiles are then hand wrapped in a choice of protective packages including foam, spiral wrappers, tissue paper, etc.
.jpg)
YOUR REQUIREMENTS, OUR SERVICE
Our one stop service is designed to take your profile from design to completion.
For finishing, this means we can do small or large runs in different colour and standard requirements. Our stock holding facility also ensures you can call react to your customer’s custom orders quickly and effectively.